Power transformers are an integral part of several electrical applications. They facilitate power transfer between two parts of an electrical circuit and create isolation while varying voltage and current. Power transformers are available in different designs and toroidal power transformers are one of them. These transformers get their name from a toroidal core that has the primary and secondary windings wound around it. When electricity is switched on, the current flows through the primary winding and induces an electromotive force (EMF) and a current in the secondary winding, thereby facilitating a swift power transfer. These transformers are widely used in various applications due to their low current leakage properties. Having said that, not all transformers of this type are built similarly. There are certain factors to look for when choosing a toroidal transformer for your application. This post analyzes a few factors that would be helpful when choosing the right transformer for your application.
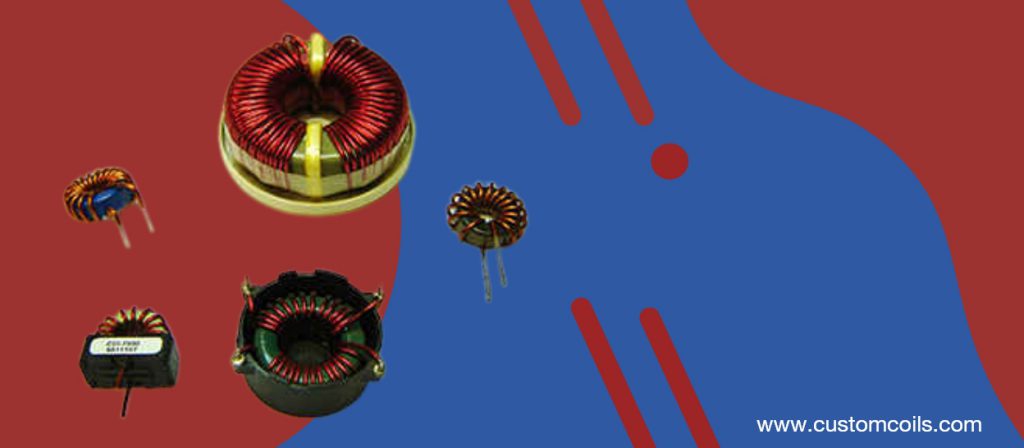
Features of a Good Toroidal Transformer You Must Know About
What is a good transformer design? The answers may vary, perhaps, the best transformer is the one that is compact-sized, lightweight, noiseless, and possesses low magnetic flux and leakage. Now, your selection would be influenced by these factors depending on your application requirements. The following pointers will help you understand it better.
- Core Material: As you may have already realized, the core forms an integral part of this transformer, so the material used must be of high quality. The following are some popular materials used for building cores.
- The core is created using ferrite materials such as cobalt, zinc, manganese, and nickel. Ferrite cores made of nickel-zinc ferrite and manganese-zinc ferrite materials are other alternatives. These core materials have low saturation flux density, permeability, and curie temperature.
- Premium-grade virgin steel is also used to make a core. A continuous strip of premium grade virgin steel is woven tightly with no air gaps to make a core. This helps avoid vibrations. Both these materials allow engineers to design transformers with a specific magnetic induction point. This helps improve their efficiency while reducing losses.
- Powdered metal cores like carbonyl iron and molybdenum permalloy are used to create a core.
- Wire Material: The wire material is known as the windings. Most toroidal transformer designs have two windings – one primary and one secondary winding. Some designs may have two secondary windings, too. These windings are made from copper and aluminum. Among these, copper is the most popular choice, but aluminum is chosen for the price advantage that it offers. Copper possesses excellent current carrying capacity as well as thermal and electrical properties.
- Material of Insulation: The safety and performance of a toroidal transformer depend on the insulation material used. Strong insulation material can build strong impact resistance and reduce the possibility of leakage and short circuits. Paper, varnish, polyester, and mineral oil are some popular insulation materials used for protecting windings. Most windings feature cellulose insulation with mineral oil.
- Techniques of Winding: The winding of the transformer plays a key role in its functioning. If not properly wound, the wire may induce leakage. Special consideration must be given to the winding technique. Bank winding technique is the most popular technique used. In this technique, the wire is wound to form a pie-shaped segment around the toroid. Equal number of odd and even segments are formed around the toroid in clockwise and counterclockwise directions. This winding is repeated until the toroid is covered completely. This type of winding helps reduce the maximum turn-in voltage stress on the conductor insulation.
- Magnetic Shielding: When compared with other types of transformers, the toroidal transformers possess low magnetic leakage. Some applications may require additional leakage protection, in such cases, an additional thin sheet of silicon steel may be used. The shielding layer is created around the circumference of the toroidal transformer and is fixed using an outer wrap.
- Encapsulation Material: Encapsulation of the transformer is done to protect it from vibrations and shocks. Thermoplastic material is usually used for encapsulating the core. Many different types of epoxies can be used to encapsulate the entire toroid transformer.
- Impregnation: Some transformers may be designed with small wire sizes and low power ratings. These transformers may be impregnated to improve their efficiency to avoid any short circuits or noise. For instance, when these transformers are used in audio applications, the toroidal core is impregnated to prevent hum.
Toroidal transformers are an integral part of voltage stabilizers, uninterrupted power supplies (UPS), lighting and radio equipment, and a wide range of medical equipment. With such an important role to play, electronic OEMs understand the importance of sourcing them from leading and experienced toroidal transformer manufacturers like Custom Coils. The company offers customized toroidal transformers which are optimized for performance with low winding resistance, low winding losses, quick heat dissipation, and low leakage inductance.