Switch mode transformers are the essential components of switch mode power supplies (SMPS). Primarily, SMPS is a complete power source, which means any electrical appliance connected to the mains. Switch mode power transformers convert AC mains power to DC output voltage. So, these are power regulating devices that either step up or down the voltage or are designed to meet the growing demand for reliable, compact, and energy-efficient power solutions. Understanding the intricacies of switch mode transformer design and manufacturing is key to grasping how modern electronics manage power conversion efficiently. This post delves into the core aspects of switch mode transformer design, highlighting its importance and the process involved in crafting these vital components.
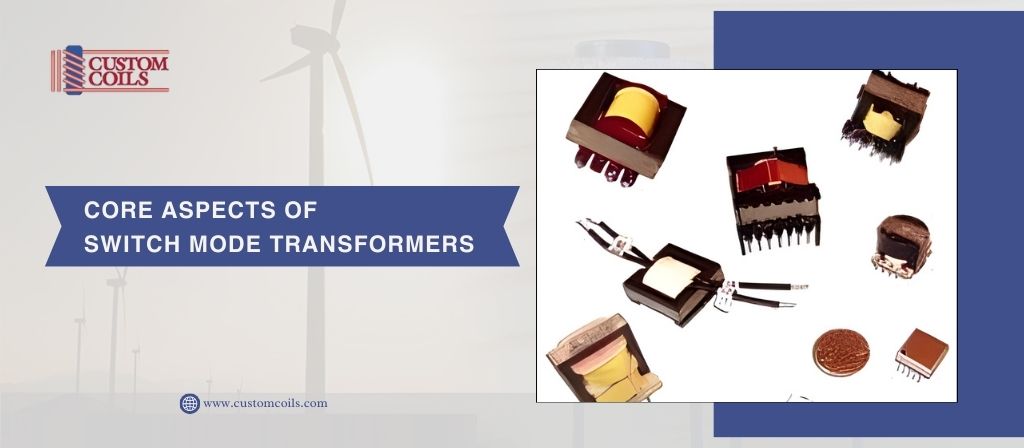
Core Aspects of Switch Mode Transformers
To understand how these transformers function, it’s essential to grasp the core aspects behind their design and operation. Below are the key aspects that drive the switch mode transformer technology:
- High-frequency operation: Switch mode transformers operate at higher frequencies. This means that they operate in the range of 10 kHz to 1 MHz.
- Isolation and conversion:> Switch mode transformers provide electrical isolation between the primary (input) and secondary (output) sides of the power supply. This is important for safety purposes and proper operation. Also, they regulate voltage levels, ensuring that the correct voltage is delivered to the load despite fluctuations in the input supply or changing load conditions.
- Low Electromagnetic Interference (EMI): Switch mode transformer designs focus on minimizing EMI through careful layout, shielding, and selection of appropriate switching components. Reducing EMI is crucial to ensure the transformer works harmoniously within a system without disrupting nearby sensitive electronics.
- Switching topology: The switching topology used in a power supply dictates how energy is stored and transferred between the input and output. The transformer’s role in these topologies is to provide the necessary isolation and voltage conversion, and its design must accommodate the specific characteristics of each topology to optimize performance.
Key Design Considerations
Several critical factors must be considered to ensure the transformer performs optimally and meets the specific needs of a power supply system. Below are some key design considerations:
- Core materials and geometry: The core material and its geometry directly influence the transformer’s efficiency and performance. For material selection, Ferrite cores work best for switch mode transformers due to their low core loss at high frequencies. Ferrites are ideal for reducing electromagnetic interference (EMI), making them a great choice for high-efficiency power conversion. The geometry of the core also impacts the transformer’s performance as it influences the magnetic flux and overall efficiency. Common core shapes such as EE, EI, and toroidal are chosen based on the specific power requirements and space constraints of the application.
- Winding techniques and insulation: The winding layout directly affects the transformer’s efficiency. It ensures proper coupling between the primary and secondary windings while reducing leakage inductance. Properly wound coils allow for optimal energy transfer between the input and output sides of the transformer. Equally important is the insulation, which safeguards the transformer from voltage spikes and thermal stress. High-quality insulation materials are used to protect the windings and ensure the transformer can withstand the demands of high-frequency switching.
- Frequency and thermal management: These are also essential design considerations. Switch mode transformers operate at much higher frequencies that help in reducing the size of the transformer. Hence, ways to dissipate heat must be considered in the design. Higher switching frequencies can increase the likelihood of heat generation, so efficient thermal management is necessary to prevent overheating and ensure reliable performance.
Manufacturing Process of Switch Mode Transformers
Below is a breakdown of the key stages involved in producing these vital components:
- Core preparation: The first step in manufacturing a switch-mode transformer is core preparation. This involves selecting the appropriate core material, usually ferrite, and shaping it as per the design specifications. The core is carefully processed to ensure the desired magnetic properties are achieved, and any imperfections or defects are removed. Once the core material is ready, it is cut or formed into the desired shape, depending on the design requirements. It is a critical stage as the core’s properties directly influence the efficiency of the transformer.
- Winding assembly: Next is winding assembly, where the copper wire is typically wound around a bobbin or form that matches the geometry of the core. These windings form the transformer’s primary and secondary windings. This process requires precision to ensure the proper number of turns, uniform winding, and correct spacing between the coils. The winding layout is carefully designed to minimize leakage inductance and maximize the efficiency of energy transfer. Proper winding is essential for ensuring that the transformer operates as expected in its final application.
- Insulation and encapsulation: Once the winding assembly is done, the transformer undergoes insulation and encapsulation. High-quality insulation materials used in windings protect them from voltage spikes and thermal stresses during operation. After insulation, the transformer is then encapsulated in a protective casing to shield the internal components from environmental factors.
- Testing and quality control: Finally, testing and quality control are critical stages in the manufacturing process. Each transformer undergoes rigorous testing to verify its performance against design specifications. This includes measuring voltage regulation, efficiency, insulation resistance, and thermal testing to ensure that the transformer can handle heat dissipation effectively.
Applications of Switch Mode Transformers
Below are some primary applications of switch-mode transformers:- Power supplies for electronics: Devices such as computers, laptops, smartphones, and tablets rely on these transformers to convert AC power from the grid into the required DC voltage.
- Telecommunication equipment: These transformers are used in power supplies for base stations, routers, and other communication infrastructure.
- Industrial equipment: Switch mode transformers power equipment where reliable voltage regulation is essential. These transformers help ensure that industrial equipment operates smoothly and efficiently, with minimal downtime or energy waste.
- Automotive systems: As the automotive industry increasingly shifts toward electric and hybrid vehicles, efficient power conversion is essential for extending battery life and improving performance. Switch mode transformers help convert and regulate the power in these systems, ensuring that vehicles operate efficiently and reliably.
- Uninterruptible Power Supplies (UPS): These transformers are used for AC to DC conversion in UPS systems provide backup power in case of power outages, rely on switch mode transformers
- Medical equipment: Medical devices like MRI, X-ray, and patient monitoring systems also use switch-mode transformers.
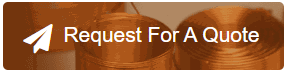
Switch mode transformers are essential components that power many of the electronic systems we rely on daily. If you are an OEM of electronic application products, you may require switch mode transformers. Custom Coils is one of the leaders in transformer solutions and offers custom options. For more information on their offerings, contact the team at 605.934.2460 or via email at sales@customcoils.com for queries or customization requirements.