Several commercial applications and electrical and electronic devices such as TVs, audio systems, and computers, comprise of transformers with various shaped cores. However, these cores present issues, like electromagnetic interference (EMI), flux leakage, and sometimes much more. Toroidal transformers were introduced to overcome these issues. Since their inception, toroidal transformers have gained immense popularity due to their compact size, lightweight, and high efficiency. A toroidal transformer has a ring-shaped core and is made from different ferromagnetic materials or conductive metals such as iron and steel of different types. Do you want to know the different core types used in the toroidal transformers? If the answer is yes, then continue reading this post to learn more about toroidal transformers.
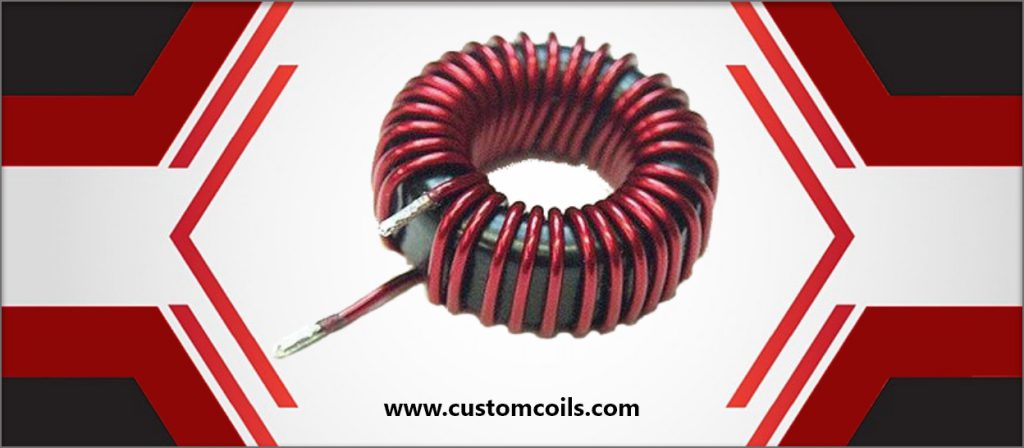
Different Core Types of Toroidal Transformers Explained
The core of the toroidal transformer is made of magnetic materials with varying levels of electrical resistivity, hysteresis, and magnetic permeability. A transformer’s efficiency mainly depends on the quality of magnetic materials. Here are some types of toroidal transformer cores. So, let’s have a look at them.
- Powdered Metal Cores: Powdered metal, usually iron powder, is the most commonly used material for constructing toroidal transformers. Powdered metal cores are made by combining grains of metal alloys with an insulating material. This mixture is then pressed into the required shape and density. The characteristics of this core type depend on two important factors – the size of the grains and the type of metal used. Carbonyl iron and molybdenum permalloy are two popular examples of powdered metal cores used in toroidal transformers.
- Laminated Iron Alloy Cores: This type of core is designed for conventional transformers that operate at low to medium frequencies. A laminated iron alloy core is constructed by rolling the metal into sheets and pressing them to get the desired shape. The stampings are then stacked in layers, which are laminated with insulating materials. The laminated construction help reduce eddy currents. Laminated cores are constructed using two material combinations or alloys – nickel-iron and silicon-iron. Silicon-iron alloys are preferred for high-power transformers. Transformers made of nickel-iron are used in high-frequency applications.
- Tape Wound Cores: They are quite similar to laminated cores. Rather than stacking donut-shaped laminations, the tape is constructed from insulated metal ribbons and wound in a spiral manner. This spiral is then encapsulated in a thin sheet, which is made either using plastic or aluminum.
- Ferrite Cores: They are one of the popular core types used for making toroidal transformers. Ferrite cores are made using a metal-oxide ceramic, iron oxide, which is then mixed with nickel, manganese, cobalt, copper, or zinc. Manganese-zinc ferrite and nickel-zinc ferrite cores are popular among these core types. These cores have gained immense popularity due to their low permeability, low Curie temperature, and their saturation flux density. One of the major benefits of ferrite cores is their high electrical resistivity which helps reduce the eddy currents.
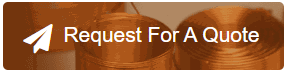
From the above information, you may have got a brief summary of core types in toroidal transformers. There are many benefits of toroidal transformers, which have contributed to their popularity. These can be used as step-up or step-down transformers in a variety of applications. Would you like to consider them for your upcoming project? If so, then you should source them from an extremely reliable company like Custom Coils. With vast years of market presence, the company specializes in manufacturing and supplying high-quality and performance-driven toroidal coil transformers. They also offer custom toroidal power transformers to meet the stringent requirement of industrial applications. Feel free to contact them at 605.934.2460 or via email at sales@customcoils.com to learn more about the custom high voltage transformers offered by them.