PRODUCTS
- High Voltage Transformers
- Switchmode Transformers
- Flyback Transformers
- Trigger Pulse Transformers
- Step Up/Down Transformers
- Power Transformers
- Toroidal Transformers
- Antennas and Air Coils
- Down Hole Applications
- DC Igniters
- High Current Inductors
- Custom Manufacturing
- Hydrogen Coils
- Control Transformers
- Inverter Transformers
- Low Profile (LPC) Transformers
- Ferrite Transformer
- Pulse Transformers
- Single Phase Transformer
- Specialty Transformers
- Isolation Transformer
- Surface Mount Transformer
- Toroidal Inductor
- Air Core Inductors
- Ferrite Inductors
- Power Inductors
- Surface Mount Inductors
Quick Contact
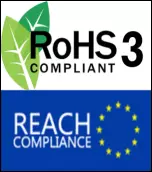
How to Improve the Efficiency of an AC or Laminated Transformer
Transformer performance depends a great deal on its efficiency. In theory, a transformer is designed to never suffer from load losses. However, in reality, transformers used in real-time applications suffer from load as well as no load losses. Loss of efficiency leads to lack of transformer performance. Hence, when facing loss problems, customers should try different types of methods to improve the efficiency of the transformer.
Improving the Efficiency of a Transformer
The following points showcase different efficiency issues that are faced by manufacturers and customers. They also showcase how suitable solutions can be utilized to address the problems.
-
Sweet Spot: This term refers to the point or area during the transformer’s operation, where the no-load losses are equal to the load losses.
- Problem: Transformer efficiency is based on complete operating load. Earlier, transformers were required to operate between 80% and 100% of the full-load rating. New changes by the Department of Energy requires the transformers to be efficient at 35% of full load.
- Solution: Manufacturers can eliminate this problem in a variety of ways. They can design the cores in larger sizes to reduce the flux density. They can utilize a higher magnetic steel grade. Manufacturers can also implement improved construction practices such as using miter joints during core lamination, or using grain-oriented electrical steel in the construction process. This can improve core loss performance, while reducing no-load core losses.
-
Increasing Inrush Current: Transformers experience inrush currents when they are turned on, either after a power outage, or after being installed.
- Problem: When transformers are energized, there is a possibility of them suffering from faults and overloading. Primary and secondary breakers are installed to protect the transformer from such issues. However, the inrush current passes only through the primary breaker, which acts as the transformer’s overcurrent protective device. This can protect the transformer, but damage the secondary breaker.
- Solution: Coordination between the breakers can help solve this issue. A simple solution is to install an oversized breaker with a low longtime pickup. This will allow both breakers to provide the requisite overload current protection, and maintain the transformer’s performance.
-
Efficiency through Size: Selecting the transformer by size is another important point to consider.
- Problem: With larger core materials, as well as an increase in the amount of copper used in the production process, transformers are delivered in large sizes. Today’s 15 kVA transformer is designed in the same size of a 30 kVA transformer that was used 10 years ago. This results in more space challenges in the application area. It also creates difficulties in terms of servicing and replacements. Incorrect transformer size can also lead to loss of efficiency.
- Solution: The reason for the large transformer sizes is spare capacity. However, it is important to understand that spare capacity on paper can result in a larger sized transformer in operation. Customers should speak to manufacturers regarding their application, and evaluate efficiency percentages before selecting transformers. This will ensure that the right sized transformer is installed, and its operational efficiency is maintained.
An understanding of the components and operation of a transformer can help customers when improving transformer efficiency. It also provides benefits when selecting a transformer for an industrial application.